Air flows, draught sealing and double glazing: how homeowners can retrofit houses for warmth
- Christopher Knaus
- Jul 5, 2022
- 4 min read
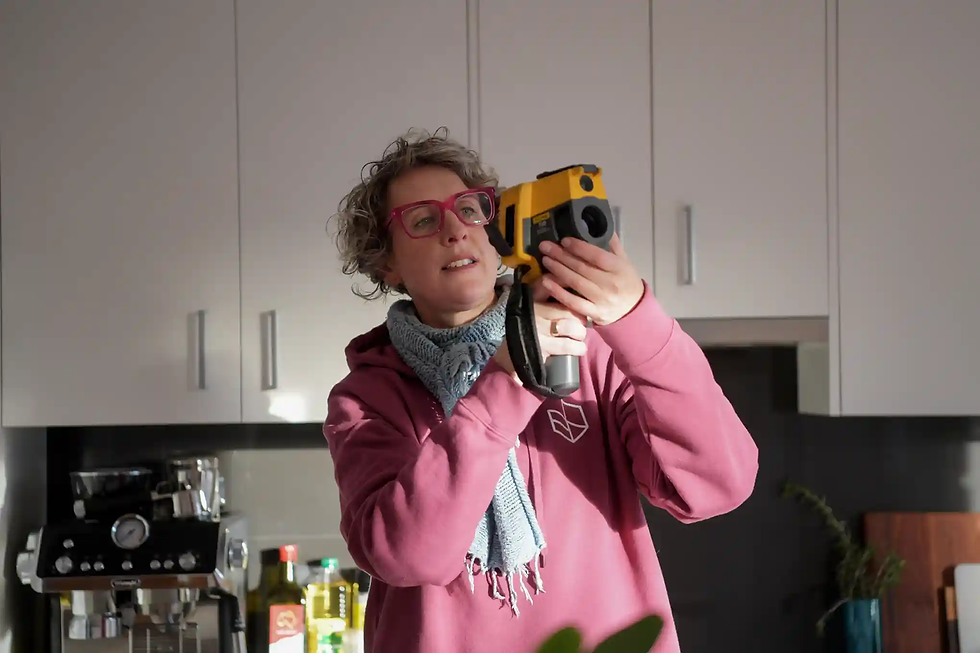
Jenny Edwards and her team of scientists assess people’s houses with thermal imaging and other high-tech tools to find tiny holes letting in the cold outside air. Photograph: Tracey Nearmy/The Guardian
Methods of keeping living spaces warm range from cheap gap-sealing to expensive double-glazing, but the first step is to find and see the problem
It’s minus four degrees when scientist Jenny Edwards arrives to inspect my bitterly cold Canberra home. Huddled inside with a coffee, dressed for an ascent to Everest base camp, I’m fretting over whether she’ll make it past the front deck. It’s iced over again.
I’m breathing fog in the kitchen and frost has covered the bay window in my bedroom.
Edwards and her technology-led, data-driven crew from Light House Architecture & Science are here to run a series of tests in an attempt to work out why the house feels so very cold. They’re going to show me the most cost-effective ways to make my house warmer.
Top of the list? Finding the tiny gaps and cracks in my home, and plugging them.
Draught sealing is by far the most cost-effective way of improving the energy efficiency of existing homes. Yet it’s barely considered by homeowners seeking flashier, more expensive solutions like rooftop solar, home batteries and new air conditioning systems.
The Light House team begin by rigging up a “blower door” – picture a red fumigation tent with a huge exhaust fan – over the back door.

The idea is to suck all the air out of my home, depressurising the interior and drawing in outside air through the walls, floors and roof.
The team can then calculate how quickly the air inside the home is being replaced and use a thermal camera to track where the cold air is coming in and – in the reverse – where my warmth is escaping.
The technology helps reveal the invisible. Like water through a sieve, the cold air streams in, often in the strangest of places.
One of the Light House assessors, Keith Jefferies, calls me over to the microwave. Above it, the blower door is sucking a cold gale straight into the house. It takes two seconds to find the source.
There’s a huge gap in the cabinetry above, which connects straight to the roof space.
“That’s where half your lovely heating is going,” Edwards says. “So lots of easy wins.”
There’s similar gaps above the fridge, behind the air conditioning unit, between the skirting boards and floorboards, around the architraves, dishwasher plumbing and old gas heating ducts, and in wardrobes. A tunnel of cold air is being sucked up through the drain in my bathroom floor.
The gaps reveal themselves as fingers of blue on the thermal camera.
By plugging in data about the dimensions and design of the building, Edwards and her team estimate the rate at which the air in my house is replaced per hour. The greater the rate, the more you have to heat your home to stay warm.
Surprisingly, it’s not as bad as I thought.
The thermal camera shows the home is decently insulated in the roof, walls and underfloor – despite some gaps – and my beautiful but terribly inefficient single-glazed colonial windows are not as leaky as we’d feared.
The results show about 21.9 air changes an hour. That’s average for Canberra homes, which record between 15 and 25 air changes an hour.
Modern European and North American homes aim for a remarkably low 1.5 to three air changes an hour.
“It has an almost linear relationship to your winter energy consumption,” she said.
The recommended standard in Australia’s national construction code is less than 10, though there’s no testing of new homes and no mandate. Edwards says she’s been to homes in Canberra that well over 30 air changes an hour.
The solutions to draught-proofing are often simple and cheap do-it-yourself jobs, such as gap-sealing around windows, floorboards and cabinetry, and blocking unused vents with chunks of foam.
Light House will steer customers towards other cheaper solutions – such as filling gaps in insulation and installing insulating blinds or curtains – before they tackle the big-ticket, more expensive solutions, including double-glazing or installing new air conditioning systems.
Most people don’t even need the kind of technology Light House uses to find the gaps in their homes.
“You don’t really need the technology to do these things,” Edwards says. “The power of it is the science of communication. Visual tools to help people feel and see the problem.”
Advertisement
That’s a good thing, because the home assessment and retrofitting industry is still tiny, despite what should be a massive market.
When Edwards found out about the blower door technology in 2008, she searched for a company that was using it on residential homes. She could find only one, thousands of kilometres away in Victoria.
More companies have since cottoned on. But Edwards says there’s still a huge awareness problem around the importance of retrofitting in lowering energy use, improving thermal efficiency, and combatting climate change.
“It drives me crazy that there are so few, and there’s so much data suggesting this is what needs to be done,” she said. “I’ve been doing it and sharing data and information and talking at conferences for a long time.”
“My feeling is that we need an army of female testers and retrofitters to go into people’s homes.”
Comments